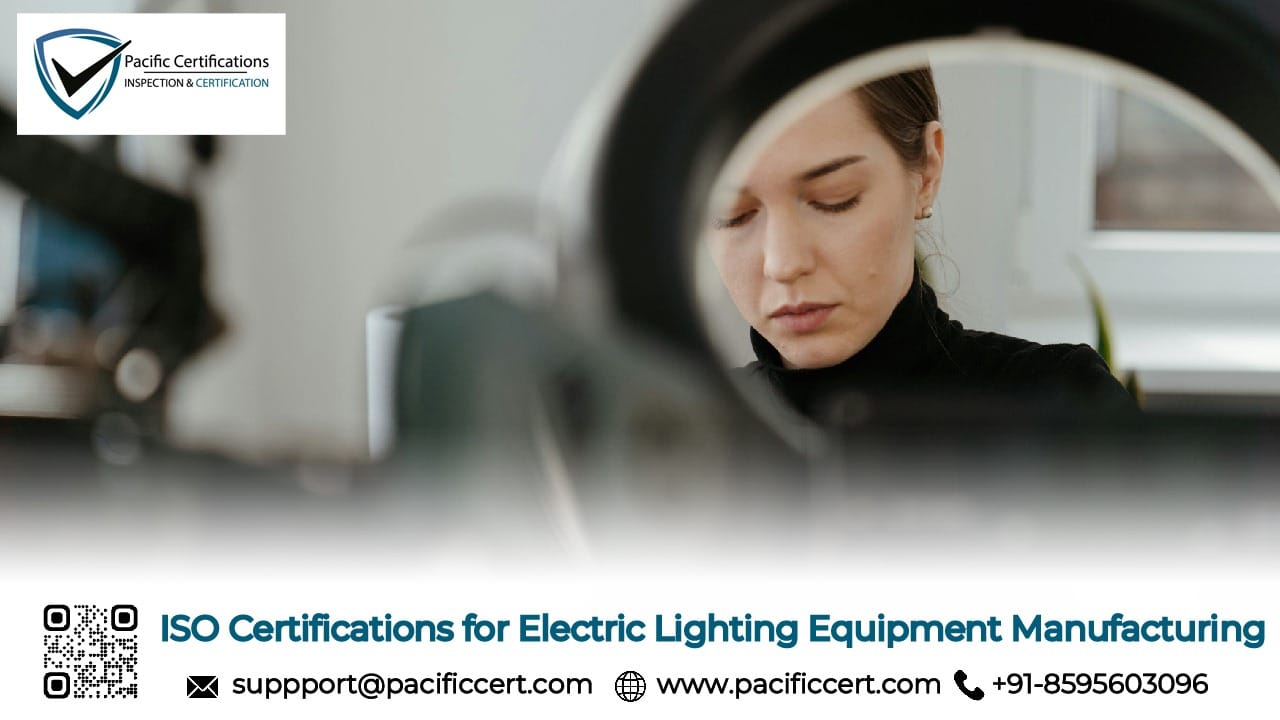
ISO certifications for Electric Lighting Equipment Manufacturing
In the Electric lighting equipment manufacturing industry, maintaining high standards in quality, safety & sustainability is paramount. ISO certifications provide a structured framework that guides manufacturers in enhancing their processes and achieving global standards. For businesses in this industry, ISO certifications ensure compliance and also create a strong foundation for growth and trust among customers.
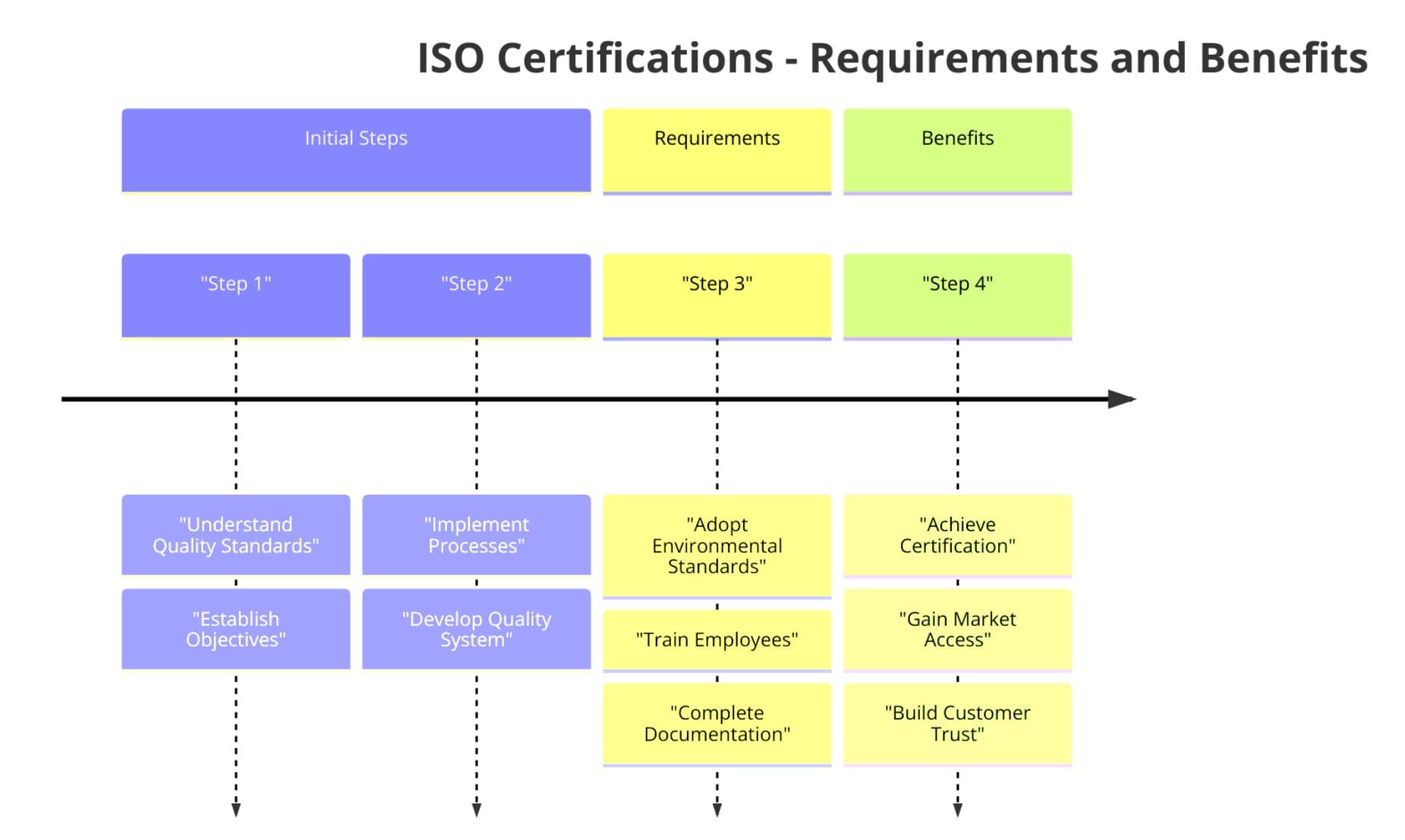
Interested in ISO certification for your Electric Lighting Equipment Manufacturing business? Reach out to us at support@pacificcert.com to learn how we can assist you.
Applicable ISO Standards for Electric Lighting Equipment Manufacturing
ISO 9001: Quality Management System: ISO 9001 is a globally recognized standard that helps companies develop an efficient quality management system (QMS). For lighting manufacturers, this standard enables the production of consistent, high-quality products and establishes a systematic approach to managing and improving quality.
ISO 14001: Environmental Management System: Environmental considerations are increasingly important for manufacturers. ISO 14001 guides companies in managing environmental responsibilities systematically, helping reduce waste, optimize resource use, and minimize environmental impact.
ISO 45001: Occupational Health and Safety: ISO 45001 sets the standard for health and safety management in the workplace. For electric lighting equipment manufacturers, adhering to this standard helps create a safer environment, reducing workplace risks and fostering a culture of safety.
ISO 50001: Energy Management System: ISO 50001 provides a framework to improve energy efficiency, crucial for manufacturing processes that involve intensive energy usage. This standard enables manufacturers to reduce energy costs and contribute to global energy-saving goals.
ISO 14064: Greenhouse Gas Emissions Management: ISO 14064 addresses the need to monitor, quantify, and reduce greenhouse gas emissions. For lighting manufacturers, following this standard aligns with global climate action goals, enhancing sustainability and corporate responsibility.
Click here to find out more applicable standards to your industry
At Pacific Certifications, we specialize in assisting companies through the ISO certification process, focusing on audits and certification issuance. Our team of experts ensures that electric lighting equipment manufacturers meet ISO standards without the challenges of self-navigation through the complex certification journey.
We streamline the process, making it easier for manufacturers to focus on their core operations while we manage the compliance aspects.
Need ISO certification for Electric Lighting Equipment Manufacturing? Our team is ready to help. Email support@pacificcert.com or call +91-8595603096 for professional guidance.
Requirements of ISO Certifications for Electric Lighting Equipment Manufacturing
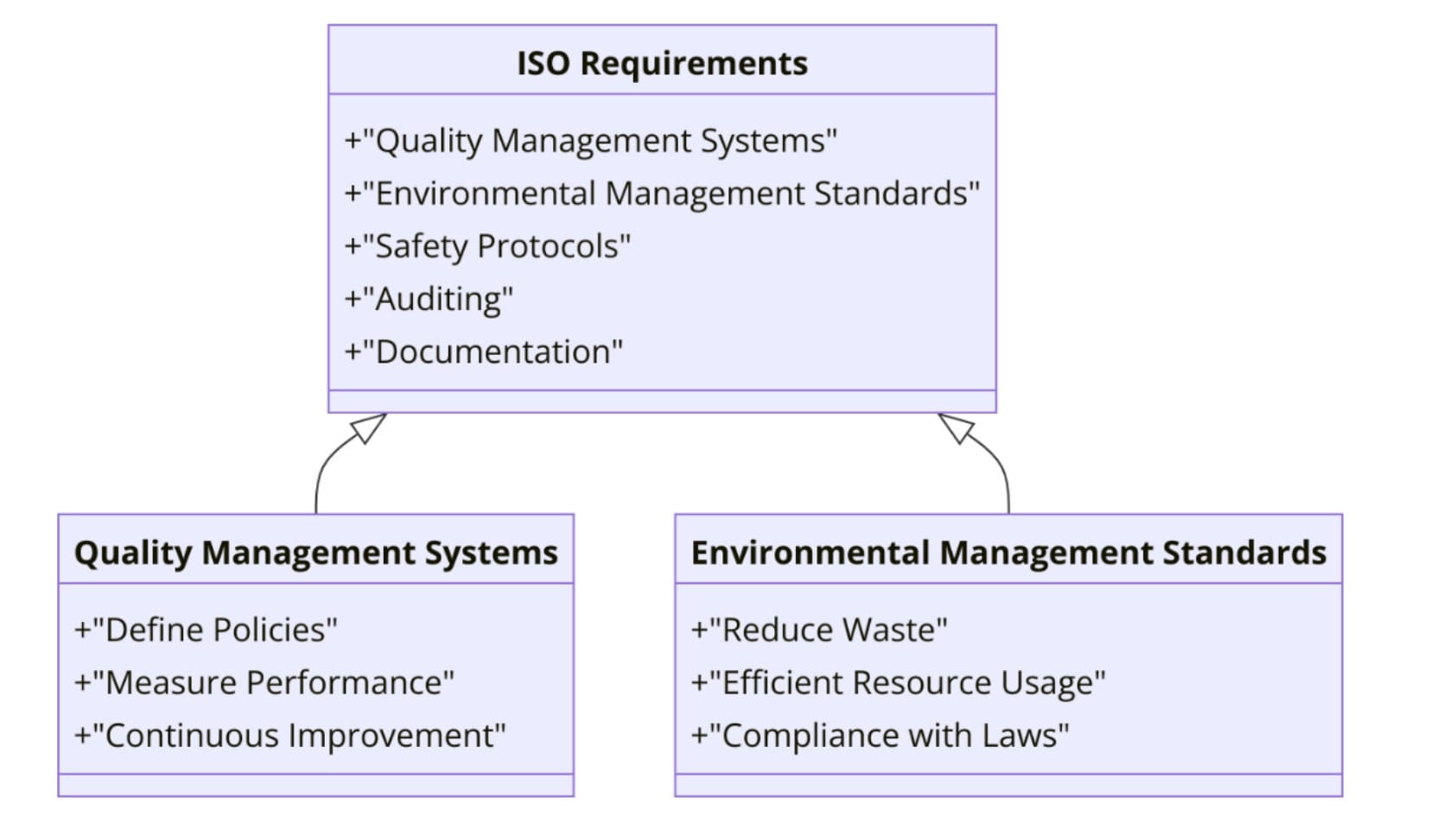
Here are the specific requirements for each ISO standard relevant to electric lighting equipment manufacturing. Each standard has unique requirements to help companies meet quality, safety, environmental, and energy efficiency goals.
ISO 9001: Quality Management System (QMS) Requirements
- Quality Policy and Objectives: Organizations need a clear quality policy aligned with their strategic goals and measurable objectives to achieve customer satisfaction.
- Process Approach: The standard requires identifying and managing interrelated processes for streamlined operations and consistency.
- Risk-Based Thinking: Companies must identify and address potential risks to prevent quality issues.
- Documented Information: Organizations must maintain documents like process flows, quality manuals, and operational records to provide transparency and accountability.
- Continuous Improvement: Implement procedures for regular reviews, audits, and improvements to the quality management system.
ISO 14001: Environmental Management System (EMS) Requirements
- Environmental Policy: Develop and maintain a policy addressing environmental goals aligned with the organization’s mission.
- Identification of Environmental Aspects and Impacts: Identify all environmental aspects and assess their potential impacts on the environment.
- Legal and Other Requirements Compliance: Ensure adherence to applicable environmental laws and regulations.
- Environmental Objectives and Plans: Set measurable goals for reducing environmental impact and establish action plans to meet these objectives.
- Operational Controls and Monitoring: Control activities that could impact the environment and monitor these for compliance with set targets.
- Emergency Preparedness and Response: Plan and prepare for environmental emergencies to mitigate adverse impacts.
ISO 45001: Occupational Health and Safety (OH&S) Management System Requirements
- OH&S Policy: Develop a policy demonstrating the organization’s commitment to health and safety at all levels.
- Hazard Identification and Risk Assessment: Identify potential hazards and assess risks to develop effective control measures.
- Legal and Regulatory Compliance: Ensure compliance with relevant health and safety regulations.
- Health and Safety Objectives: Establish and work towards specific health and safety targets to improve workplace conditions.
- Employee Training and Participation: Engage employees in health and safety initiatives, including regular training and feedback.
- Monitoring, Measurement, and Continuous Improvement: Regularly assess the effectiveness of the OH&S management system and make improvements as needed.
ISO 50001: Energy Management System (EnMS) Requirements
- Energy Policy: Develop an energy policy to outline the organization’s commitment to energy efficiency and performance.
- Energy Planning and Baseline Establishment: Establish a baseline and collect data to analyze energy consumption patterns.
- Energy Objectives and Targets: Set measurable energy efficiency goals and action plans to achieve them.
- Energy Review: Conduct reviews to identify areas for improving energy efficiency.
- Operational Controls and Design: Implement controls over energy-consuming activities and incorporate energy-efficient designs in new processes.
- Performance Monitoring and Measurement: Regularly monitor energy usage and measure improvements against the baseline.
These standards form a structured approach that helps manufacturers of electric lighting equipment achieve quality, safety, environmental, and energy management objectives, enhancing both efficiency and corporate responsibility.
Ensure compliance and quality in your electric lighting equipment manufacturing process. For ISO certification, contact us at support@pacificcert.com.
Benefits of ISO Certifications for Electric Lighting Equipment Manufacturing
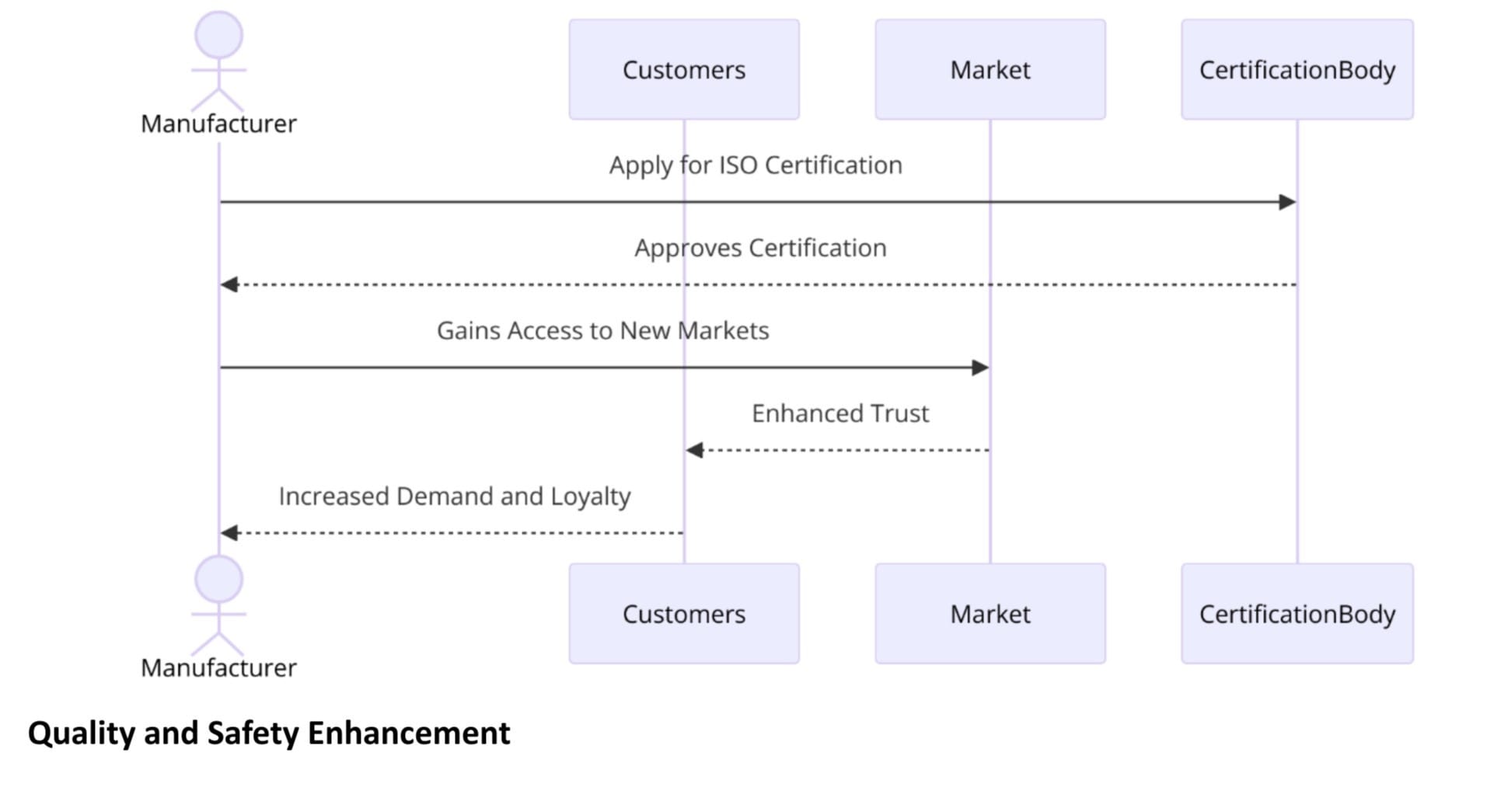
ISO certifications offer numerous benefits, helping manufacturers improve product quality, reduce environmental impact, and enhance efficiency.
Quality and Safety Enhancement: Through ISO 9001 and ISO 45001, manufacturers improve their production processes, ensuring high-quality and safe products for consumers. This builds customer trust and elevates brand reputation.
Environmental Benefits through ISO 14001: Implementing ISO 14001 helps manufacturers minimize their environmental footprint by reducing waste and managing resources responsibly. This not only meets regulatory demands but also appeals to eco-conscious consumers.
Cost Savings and Efficiency with ISO 50001: With ISO 50001, manufacturers can optimize energy use, lowering operational costs and supporting global sustainability goals. This standard promotes efficient energy management, which translates to significant cost savings over time.
In 2024, the electric lighting equipment manufacturing industry is seeing a shift toward energy-efficient solutions and sustainable practices. Technological innovations, such as LED advancements and smart lighting systems, are shaping the future of lighting.
With global emphasis on carbon reduction and energy savings, manufacturers are prioritizing ISO certifications to demonstrate their commitment to environmental responsibility and operational efficiency. The rise in consumer demand for sustainable products further underscores the need for adherence to ISO standards.
Contact us today to discuss how ISO certification can elevate your operations and set you apart in the industry!
Pacific Certifications is accredited by ABIS, in case you need support with ISO certification for your Electric Lighting Equipment Manufacturing business, please contact us at support@pacificcert.com or +91-8595603096.
FAQs: ISO Certifications for Electric Lighting Equipment Manufacturing
How does ISO certification impact electric lighting equipment manufacturing?
ISO certification ensures that manufacturers adhere to global standards, improving product quality, safety, and environmental impact, which enhances customer trust.
What are the costs associated with ISO certification?
Costs vary based on the standard and the scope of certification. Contact us for a detailed quote tailored to your manufacturing needs.
How long does it take to achieve ISO certification?
The certification timeline depends on the readiness and size of the organization. Typically, it ranges from a few months to a year.
Which ISO standard is most critical for electric lighting equipment manufacturers?
ISO 9001, focusing on quality management, is particularly important for ensuring high standards in product manufacturing.
Do ISO certifications have an expiration?
Yes, ISO certifications usually last for three years, after which companies must undergo a recertification audit to maintain their status.
How often do we need to renew our ISO certification?
Certifications require renewal every three years, with annual surveillance audits conducted in the interim.
Read More at: Blogs by Pacific Certifications
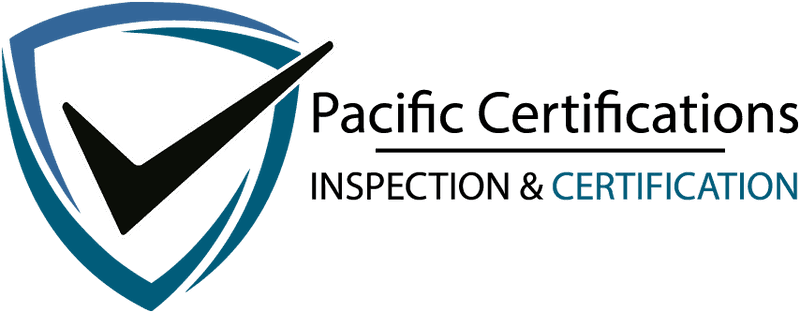