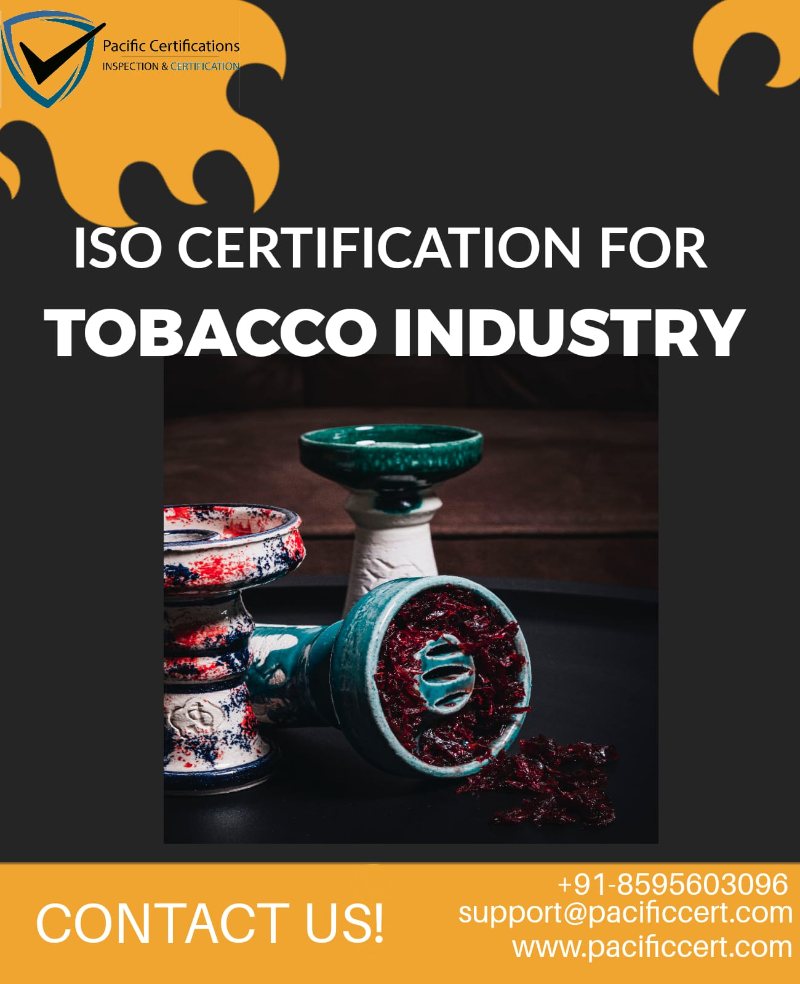
ISO Certification for Tobacco Industry
ISO certifications play a critical role in the tobacco industry by ensuring compliance with quality, safety, and environmental standards. ISO 9001 for Quality Management Systems helps tobacco companies streamline their production processes, ensuring that products meet consistent quality standards from raw material sourcing to packaging and distribution. This certification helps improve efficiency, reduce waste, and enhance customer satisfaction. ISO 14001 for Environmental Management is essential for managing the environmental impact of tobacco production, including waste management, emissions control, and sustainable resource use. Additionally, ISO 45001 for Occupational Health and Safety is vital for ensuring safe working conditions in manufacturing environments where employees are exposed to chemicals and machinery. These certifications help the tobacco industry meet regulatory requirements, build trust with consumers, and demonstrate a commitment to sustainability and operational excellence.
For ISO certification support for the tobacco industry, contact support@pacificcert.com.
ISO (International Organization for Standardization) offers various standards that cover a wide range of industries and sectors, including the tobacco industry. The tobacco industry can benefit from ISO certifications to ensure quality, safety, and environmental responsibility in their processes and products. Some relevant ISO standards for the tobacco industry include:
ISO 9001: Quality Management System (QMS)
ISO 14001: Environmental Management System (EMS)
ISO 45001: Occupational Health and Safety Management System (OHSMS)
ISO 22000: Food Safety Management System
ISO 26000: Social Responsibility
ISO 17025: Testing and Calibration Laboratories
An ISO certification demonstrates a commitment to quality, safety, and responsible practices. Organizations seeking ISO certification typically need to undergo an assessment process by a third-party certification body.
Before pursuing ISO certification, it's recommended to thoroughly understand the specific standards that apply to your operations within the tobacco industry and to work with experienced consultants or certification bodies to ensure a successful certification process. Keep in mind that regulations and standards can evolve over time, so it's essential to stay updated on the latest requirements in your region and industry.
Applicable ISO standards for Tobacco Industry
The tobacco industry can benefit from implementing various ISO standards to ensure quality, safety, and environmental responsibility in their processes and products. Here are some applicable ISO standards for the tobacco industry:
ISO 9001: Quality Management System (QMS) This standard provides a framework for implementing a quality management system that focuses on customer satisfaction, continuous improvement, and consistent product quality.
ISO 14001: Environmental Management System (EMS) ISO 14001 helps organizations establish an environmental management system to monitor and reduce their environmental impact, manage waste, and promote sustainable practices.
ISO 45001: Occupational Health and Safety Management System (OHSMS) ISO 45001 assists in managing occupational health and safety risks, creating safe working conditions, and complying with relevant regulations to protect employees and stakeholders.
ISO 22000: Food Safety Management System If the tobacco industry involves products with food-related components (such as flavored tobacco), ISO 22000 ensures safe production, handling, and distribution while managing food safety risks.
ISO 26000: Social Responsibility ISO 26000 provides guidance on social responsibility, helping organizations address the social, ethical, and societal implications of their activities, including the potential health and societal impacts of tobacco products.
ISO 17025: Testing and Calibration Laboratories If the tobacco industry requires testing and analysis, ISO 17025 ensures the competence, accuracy, and reliability of testing laboratories' operations.
ISO 31000: Risk Management ISO 31000 offers principles and guidelines for effective risk management, which can be valuable for addressing various risks associated with the tobacco industry, including regulatory, health, and market risks.
ISO 10002: Customer Satisfaction and Complaints Handling ISO 10002 outlines best practices for handling customer complaints and improving customer satisfaction, which can be useful for addressing customer concerns related to tobacco products.
ISO 14064: Greenhouse Gas Emissions If the tobacco industry aims to measure and manage its carbon footprint, ISO 14064 provides guidelines for quantifying and reporting greenhouse gas emissions.
Choice of ISO standards to implement depends on the specific activities, products, and services of your organization within the tobacco industry. Engaging with a professional consultant or certification body can help you identify the most relevant standards and guide you through the certification process.
Pacific Certifications is accredited by ABIS If you need more support with an ISO certification for your business in Tobacco Industry, please contact us at +91-8595603096 or support@pacificcert.com
Requirements of ISO Certification for Tobacco Industry
ISO certification involves adhering to specific requirements outlined in the relevant ISO standards. For the tobacco industry, the requirements may vary based on the standards chosen. Here's a general overview of what's typically involved in obtaining ISO certification for the tobacco industry:
Select Appropriate Standards: Identify the ISO standards that are most relevant to your operations within the tobacco industry. This could include standards like ISO 9001, ISO 14001, ISO 45001, ISO 22000, and others, depending on your organization's focus and scope.
Gap Analysis: Conduct a thorough assessment of your current processes and practices against the requirements of the chosen ISO standards. Identify gaps that need to be addressed to meet the standards.
Develop Implementation Plan: Create a detailed plan for implementing the necessary changes to align with the ISO standards. This might involve updating processes, policies, documentation, and training programs.
Documentation: Develop the required documentation to demonstrate compliance with the ISO standards. This includes quality manuals, procedures, work instructions, and records.
Training and Awareness: Train your employees on the ISO standards and their roles in implementing the changes. Raise awareness about the importance of quality, safety, and environmental responsibility.
Implementation of Changes: Implement the changes outlined in your plan, such as quality control measures, environmental management practices, safety protocols, and more.
Internal Audits: Conduct internal audits to assess whether your organization's processes and practices align with the ISO standards. Identify areas for improvement and take corrective actions.
Management Review: Hold regular management reviews to evaluate the progress of your ISO implementation and to ensure that the management team is actively involved in the process.
Corrective and Preventive Actions: Address any non-conformities or issues identified during internal audits by implementing corrective and preventive actions.
External Audit: Engage a third-party certification body to perform an external audit of your organization's processes and practices against the chosen ISO standards.
Certification Decision: Based on the results of the external audit, the certification body will determine whether your organization meets the requirements of the ISO standards and issue the certification if successful.
Continual Improvement: Maintain and continually improve your systems and processes to ensure ongoing compliance with the ISO standards and to achieve better performance.
ISO certification process takes time, effort, and resources. Organizations seeking certification should have a strong commitment to quality, safety, and environmental responsibility.
Benefits of ISO Certification for Tobacco Industry
Obtaining ISO certification in the tobacco industry can bring numerous benefits to your organization, including enhanced credibility, improved processes, and increased customer trust. Here are some key benefits of ISO certification for the tobacco industry:
Credibility and Reputation: ISO certification demonstrates your commitment to quality, safety, and responsible practices. It enhances your organization's reputation and credibility among customers, stakeholders, and regulatory authorities.
Global Recognition: ISO standards are internationally recognized and respected. Certification indicates that your organization meets globally accepted benchmarks for quality, safety, and environmental responsibility.
Market Access and Compliance: ISO certification can help you meet regulatory requirements and access new markets. Many markets require ISO certification as a prerequisite for doing business, giving you a competitive advantage.
Process Improvement: Implementing ISO standards requires a thorough evaluation and improvement of your processes. This can lead to increased efficiency, reduced waste, and optimized resource utilization.
Risk Management: ISO standards often incorporate risk management principles. By identifying and addressing potential risks, you can mitigate adverse impacts on your operations and reputation.
Customer Satisfaction: ISO certification emphasizes customer satisfaction and continuous improvement. Improved processes lead to better products and services, resulting in higher customer satisfaction and loyalty.
Employee Engagement: ISO standards encourage involvement from all levels of the organization. Engaging employees in the certification process can foster a sense of ownership, accountability, and teamwork.
Health and Safety: ISO 45001 certification (Occupational Health and Safety Management System) enhances workplace safety and reduces the risk of accidents, contributing to a healthier and more productive workforce.
Environmental Responsibility: ISO 14001 certification (Environmental Management System) promotes environmentally friendly practices, reducing your environmental impact and meeting the growing demand for sustainable products.
Legal and Regulatory Compliance: ISO certification can assist in demonstrating compliance with various legal and regulatory requirements related to quality, safety, and the environment.
Supplier and Partner Relationships: ISO certification can strengthen relationships with suppliers and partners, as they gain confidence in your organization's ability to deliver consistent quality and meet contractual obligations.
Continuous Improvement: ISO certification is not a one-time achievement. It encourages a culture of continuous improvement, ensuring that your organization evolves to meet changing industry standards and customer expectations.
Transparent Communication: ISO-certified organizations often communicate their commitment to quality and safety to customers, which can positively impact buying decisions.
Cost Savings: Improved processes, reduced waste, and better resource management can lead to cost savings over time.
Public Relations: ISO certification provides a positive story to share with the public and media, showcasing your dedication to responsible practices and contributing to a positive public image.
In the tobacco industry, where social and health considerations are important, ISO certification can help address concerns related to the societal impact of tobacco products. It's essential to choose the most relevant ISO standards for your organization's goals and operations to maximize these benefits.
If you need more support with ISO Certification for your business in Tobacco Industry, please contact us at +91-8595603096 or support@pacificcert.com
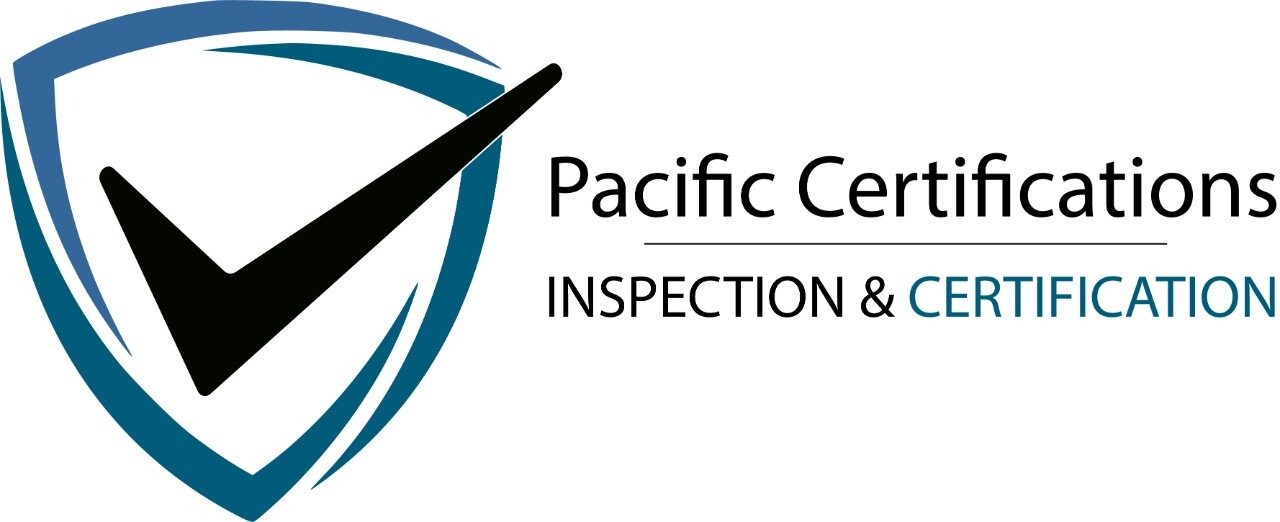
Read more: ISO Certification for Textile Industry-Related standards-Requirements-Benefits