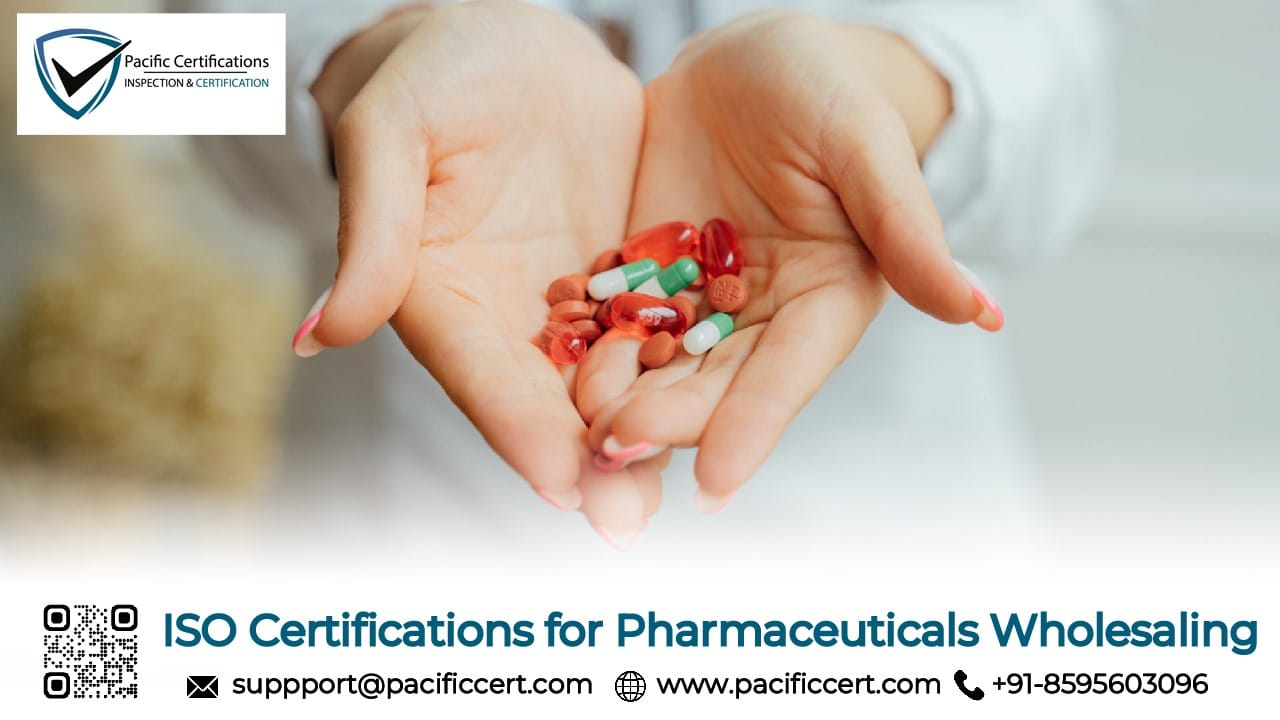
ISO Certifications for Pharmaceuticals Wholesaling
The pharmaceutical industry is one of the most heavily regulated industries in the world including pharmaceuticals wholesaling. Wholesalers play important role in the pharmaceutical supply chain, ensuring that medicines reach healthcare providers and pharmacies in a timely and safe manner.
Given the nature of the products being handled, life-saving drugs and critical medical supplies, it is essential that these companies comply with the highest quality, safety and management standards. This is where ISO certifications become invaluable.
ISO standards are internationally recognized frameworks that ensure organizations operate efficiently and in a manner that meets regulatory requirements. Obtaining ISO certification for pharmaceutical wholesalers, means compliance with stringent guidelines regarding the storage, transportation & distribution of medicines.
It provides a structured approach to risk management, ensuring that operations meet global best practices.
If you are looking for ISO certification for Pharmaceuticals Wholesaling, contact us today at support@pacificcert.com or call +91-8595603096.
Applicable ISO Standards for Pharmaceuticals Wholesaling
There are several ISO standards that are directly applicable to pharmaceutical wholesalers. These standards cover various aspects of quality & security. The following are the most relevant ISO standards for this industry:
ISO 9001:2015 – Quality Management System (QMS)
ISO 9001 is the globally recognized standard for quality management systems. ISO 9001 helps pharmaceutical wholesalers to ensure that the processes for storing, distributing, and managing pharmaceuticals are optimized for quality.
ISO 13485:2016 – Medical Devices
ISO 13485 is highly relevant to wholesalers who also deal with medical equipment or consumables. The standard ensures compliance with stringent regulatory requirements related to the quality, safety, and performance of medical devices.
ISO 45001:2018 – Occupational Health and Safety Management System (OHSMS)
ISO 45001 is the international standard for health and safety management systems. Given the hazardous nature of handling and storing certain pharmaceutical products, this standard ensures that wholesalers maintain a safe working environment for their employees.
ISO 27001:2022 – Information Security Management System (ISMS)
ISO 27001 helps pharmaceutical wholesalers protect sensitive information, such as customer data and supply chain details. This standard establishes processes for managing the confidentiality, integrity, and availability of data, which is particularly crucial for avoiding breaches and ensuring regulatory compliance with data protection laws.
ISO 22301:2019 – Business Continuity Management System (BCMS)
ISO 22301 ensures that wholesalers are prepared to handle disruptions, such as natural disasters, cyberattacks, or pandemics. This standard ensures that businesses have a continuity plan in place to minimize downtime and continue operations in times of crisis.
Click here to find out more applicable standards to your industry
For expert assistance with ISO certification for your pharmaceutical wholesale business, reach out to us via support@pacificcert.com.
At Pacific Certifications, we specialize in providing audit and certification services for a wide range of ISO standards. Our team of experienced auditors is committed to helping you achieve compliance with international standards that align with your operational needs.
Our role is strictly focused on conducting thorough audits and certifying that your processes meet the requirements of the relevant ISO standards.
Requirements of ISO Certifications for Pharmaceuticals Wholesaling
ISO 9001:2015 – Quality Management System (QMS)
- Context of the Organization: Understanding the internal and external factors that affect the organization’s ability to achieve the intended results of its quality management system.
- Leadership: Demonstrating leadership and commitment to implementing the QMS. Top management must take responsibility for establishing and maintaining the QMS, along with a clear quality policy.
- Planning: Identifying risks and opportunities related to quality objectives and planning actions to address them. Establish measurable quality objectives that align with the organization's strategy.
- Support: Providing the necessary resources, including competent personnel, infrastructure, and a suitable environment for the operation of processes.
- Operation: Ensuring that operational processes are consistent with the organization’s quality management objectives. This includes planning, controlling, and verifying processes for product and service delivery.
- Performance Evaluation: Monitoring, measuring, analyzing, and evaluating the performance of the QMS. This includes conducting internal audits and reviewing customer feedback.
- Improvement: Continuous improvement of the QMS based on the analysis of performance data and corrective actions.
ISO 13485:2016 – Medical Devices Quality Management System
While focused on medical devices, ISO 13485 can be applicable for pharmaceutical wholesalers handling medical equipment. Key requirements include:
- QMS Documentation: Establishment and maintenance of a quality management system that is appropriately documented and maintained throughout the product lifecycle, especially for medical devices.
- Risk Management: A systematic risk management approach throughout the lifecycle of the medical device, from product development to delivery, ensuring that risks are minimized.
- Design and Development Controls: Ensuring that all medical devices and related products are designed and developed in accordance with customer requirements and regulatory obligations.
- Product Realization: Ensuring that the necessary processes are in place for the consistent realization of the medical device, including proper documentation, traceability, and validation.
- Compliance with Regulatory Requirements: Meeting international regulatory requirements concerning medical devices, including market surveillance and post-market obligations.
- Customer Satisfaction: Consistently meeting customer requirements regarding the safety, performance, and quality of medical devices.
- Continuous Improvement: Implementing a system for continual improvement of the quality management system based on audits, corrective actions, and feedback.
ISO 45001:2018 – Occupational Health and Safety Management System (OHSMS)
- Hazard Identification and Risk Assessment: Identifying potential hazards in the workplace, assessing the risks associated with those hazards, and implementing controls to reduce risks.
- Health and Safety Policies: Implementing health and safety policies that outline the organization’s commitment to protecting employees and stakeholders from occupational hazards.
- Compliance Obligations: Ensuring compliance with applicable legal and regulatory requirements regarding occupational health and safety.
- Participation and Consultation: Encouraging active participation from employees at all levels in health and safety matters, ensuring that their input is considered in decision-making.
- Operational Controls: Implementing and maintaining controls related to occupational health and safety risks. This may include workplace safety protocols, emergency response plans, and safety training.
- Performance Evaluation: Monitoring and evaluating the effectiveness of the occupational health and safety management system through audits, inspections, and employee feedback.
- Incident Reporting and Investigation: Establishing a process for reporting, investigating, and analyzing workplace incidents to prevent reoccurrence.
- Continual Improvement: Continuously improving the occupational health and safety management system by identifying and addressing non-conformities, conducting audits, and implementing corrective actions.
ISO 27001:2022 – Information Security Management System (ISMS)
- Information Security Policy: Developing and maintaining an information security policy that aligns with organizational objectives and protects sensitive data.
- Risk Assessment and Treatment: Identifying information security risks and implementing a risk management process. This includes risk identification, risk assessment, and the application of appropriate controls to mitigate risks.
- Asset Management: Proper management of information assets, ensuring that they are appropriately classified, secured, and managed throughout their lifecycle.
- Access Control: Establishing controls to manage access to information, ensuring that only authorized personnel can access sensitive data.
- Incident Management: Implementing an information security incident management process to detect, respond to, and recover from security breaches or incidents.
- Compliance with Legal and Regulatory Requirements: Ensuring that the organization complies with legal, regulatory, and contractual obligations related to information security.
- Training and Awareness: Providing regular training to employees and relevant stakeholders on information security practices and policies.
- Monitoring and Review: Continuously monitoring, measuring, and reviewing the effectiveness of the information security management system through internal audits and performance evaluations.
- Continuous Improvement: Establishing a process for the continual improvement of the information security management system.
Each of these ISO standards has its unique focus, but collectively they provide a strong framework for managing quality and safety within an organization. Pharmaceutical wholesalers, in particular, benefit from implementing these standards to maintain compliance and enhance overall risk management.
To ensure your pharmaceutical wholesale business meets international standards, contact us for ISO certification at support@pacificcert.com or call +91-8595603096.
Benefits of ISO Certifications for Pharmaceuticals Wholesaling
Achieving ISO certification offers numerous benefits for pharmaceutical wholesalers. These benefits extend beyond mere compliance, helping companies improve their customer satisfaction and reputation. Here are some of the key advantages:
- For pharmaceutical wholesalers, achieving ISO certification enhances their credibility with customers, suppliers, and regulatory bodies.
- By implementing ISO standards, companies can streamline their operations, leading to greater efficiency and reduced operational costs.
- Standards like ISO 27001 and ISO 22301 help pharmaceutical wholesalers manage risks related to data security and business continuity.
- By focusing on quality management and continual improvement, pharmaceutical wholesalers can enhance their service delivery, leading to increased customer satisfaction and loyalty.
- ISO certifications ensure that pharmaceutical wholesalers comply with international and local regulations.
For reliable ISO certification services for Pharmaceuticals Wholesaling, contact Pacific Certifications at support@pacificcert.com or call +91-8595603096.
Market Trends
As the pharmaceutical industry continues to grow, the role of wholesalers is becoming increasingly critical. In this year, there has been a heightened focus on digitization and automation within the pharmaceutical supply chain.
Companies are adopting advanced technologies to improve efficiency, track shipments, and ensure the integrity of temperature-sensitive products.
Furthermore, the rise of personalized medicine is pushing wholesalers to adapt to new distribution models that can handle smaller, more frequent shipments of specialized drugs.
Research indicates that the global pharmaceutical wholesale market is expected to grow at a compound annual growth rate (CAGR) of over 6% from 2023 to 2028. This growth is fueled by increasing demand for prescription drugs, the rise of chronic diseases, and the expanding global population.
For pharmaceutical wholesalers, obtaining ISO certifications can help them stay competitive in this fast-growing market by ensuring that their processes meet the highest standards of quality and efficiency.
If you're a pharmaceutical wholesaler looking to enhance your operational efficiency, improve compliance, and boost your reputation, ISO certification is the way forward. Our experienced team is ready to guide you through the certification process, ensuring that your business meets international standards.
Pacific Certifications is accredited by ABIS, in case you need support with ISO certification for your Pharmaceuticals Wholesaling business, please contact us at support@pacificcert.com or +91-8595603096.
FAQs: ISO Certifications for Pharmaceuticals Wholesaling
1. What is ISO 9001, and why is it important for pharmaceutical wholesalers?
ISO 9001 is the international standard for quality management systems. It helps pharmaceutical wholesalers ensure that their operations are optimized for quality and efficiency, leading to improved customer satisfaction and regulatory compliance.
2. How long does it take to get ISO certified?
The time frame for ISO certification varies depending on the size of your organization and the specific standard you're pursuing. Typically, it can take anywhere from a few months to a year to complete the certification process.
3. Do I need to get all applicable ISO certifications for my wholesale business?
While it is not mandatory to obtain every applicable ISO certification, it is recommended to pursue the ones that align with your business needs and regulatory requirements. For example, ISO 9001 is essential for quality management, while ISO 27001 is important if you handle sensitive data.
4. Can Pacific Certifications provide consultancy services for ISO certifications?
No, we do not offer consultancy services. Our role at Pacific Certifications is strictly focused on auditing and issuing certifications. We do not engage in gap analysis, training, or implementation.
5. How can ISO certification improve my business’s efficiency?
ISO certification encourages businesses to document their processes, identify inefficiencies, and implement continuous improvement measures. This leads to optimized operations, reduced waste, and improved overall efficiency.
Read More at: Blogs by Pacific Certifications
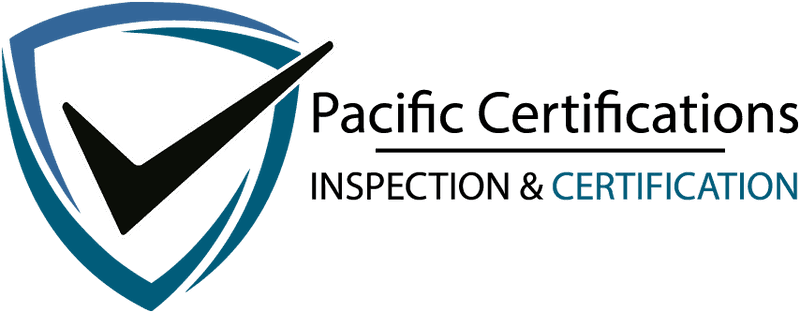